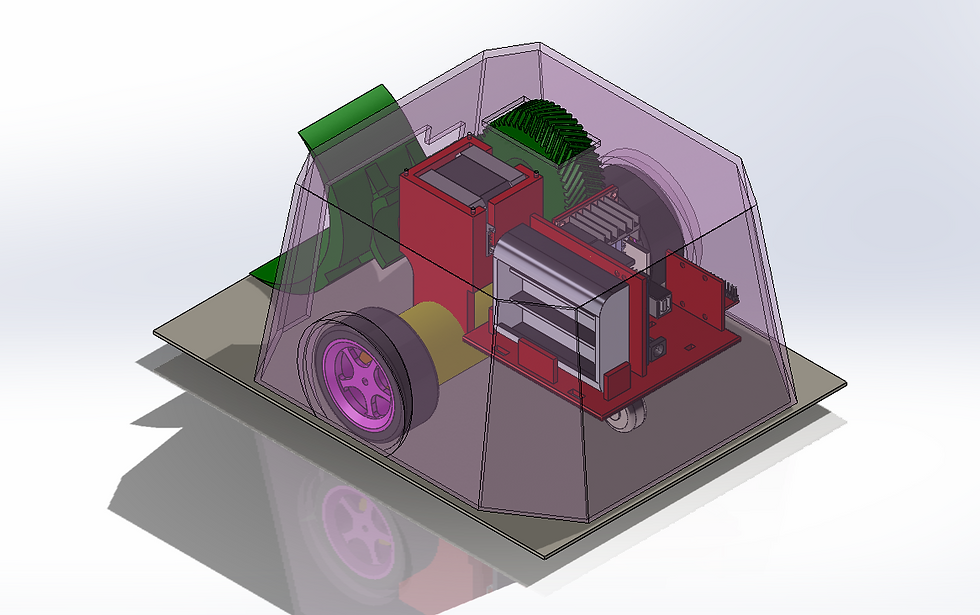
During this competition the challenge was to build a robot that could push other robots out of a circular arena while resisting being pushed out as well. The robots also had to have a smaller length-width cross section than a piece of printer paper and remain under 5 pounds. I was put in charge of design and manufacturing of the robot for this 3 month long project.
My group's main strategy for the design was to incorporate a hard outer shell (which is how we got our team name... the Koopahs), which would hopefully provide a good defense against other team's attacks. For offense, we wanted to incorporate a shovel type mechanism that could reach under other team's vehicles, and scoop them off the ground. This would reduce their contact (and friction) with the ground, hopefully making it easier to drive them out of the circle.
With these deliverables and restraints in mind, I started by picking the parts for this robot. I knew we could make use of 2 12V DC motors for driving. I also knew that our design was too advanced to focus on build a drive shaft, so I opted to make our third point of contact with the ground a caster wheel. This way we need only to slow down one wheel and keep the other spinning at a faster rate to move. With the DC motors came a L298N DC motor driver.
Our developer board for this project was an Arduino Uno R3. we needed the larger board to handle all of the analog/digital input and output for this project.
To operate the shovel mechanism, I decided to use a Nema 17 stepper motor and gears to increase torque output. The advantages of a stepper motor here are that we are able to precisely move a certain number of steps up and that same number of steps back down (leading to a constant attack movement). An A4988 motor driver was used to control the stepper motor movements.
To accept input for controlling the bot, we used an HM-10 Bluetooth module and my 3 other teammates developed an app with an interface to control the bot.
I then modelled each of the parts that we were using and began designing custom parts to build a cohesive robot with each of the functionalities outlined.
This project wasn't too challenging thanks to my experience building my own robot arm. For this reason, I decided to add the gears to the Nema motor to learn how to design more advanced parts. I also tried to push the boundaries of my 3D printer by combining a lot of complex 3D bodies into a single part (whereas I usually split the part into many pieces that are easier to print and fix them together in post processing).
My final design is shown below. I am currently in the process of printing all of the parts (and iterating on the design to improve tolerances of measurements).

Comments